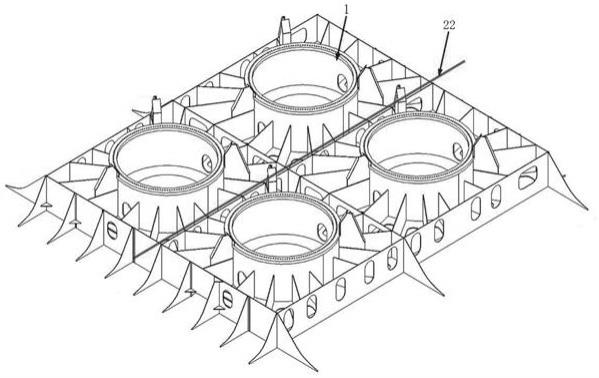
1.本发明属于钢结构建筑技术领域,具体为田字型海上风电塔筒运输船用托架及其施工工艺
。
背景技术:2.田字型海上风电塔筒运输船用托架由四个“星”型结构组成,每个“星”型结构由中心筒体和
16
块加劲板腿组合焊接而成
。
筒体截面为
φ
7016x60x2500mm
的圆管,与法兰截面为
φ
7176x192mm
,宽度
473mm
的圆环法兰焊接
。
圆管直径大,厚度大,精度要高,焊接过程中变形控制难
。
3.cn 218117966 u
公开的一种防止风电塔筒变形的起吊装置,安装板位于塔筒的后侧且与设于塔筒端面处的法兰盘相贴,安装板的前端设有伸入塔筒内侧的支撑组件,支撑组件与塔筒的内侧壁相抵,支撑组件包括筒体和多个支撑单元,支撑单元包括伸缩杆和垫板,伸缩杆与筒体的中轴线相互垂直,伸缩杆的外套管与筒体连接,其内套杆与其对应垫板的一端连接,垫板的另一端与塔筒的内侧壁相抵
。
通过多组伸缩杆和垫板对塔筒进行支撑,但是该支撑结构在支撑时需要对伸缩杆的伸长量进行控制,防变形的操作比较麻烦
。
4.为此,需要一种新的技术方案以解决上述技术问题
。
技术实现要素:5.本发明所要解决的技术问题是提供一种降低制造难度,能够在焊接过程中很好地控制构件变形的田字型海上风电塔筒运输船用托架及其施工工艺
。
6.为了解决以上技术问题,本发明提供田字型海上风电塔筒运输船用托架,包括四个相接的星型结构,每个星型结构由中心的筒体和加强筋板组装而成;筒体设置在法兰板上,筒体内下部设置顶隔板,顶隔板上设有加劲条,形成筒体合拢件;筒体合拢件通过底封板设置在底板上;底板的横向边上设置通长腹板,纵向相接处设置中间腹板,两侧边设置侧板;筒体外壁通过加强筋板与中间腹板
、
侧板
、
通长腹板连接;侧板
、
通长腹板上设置盖板,筒体穿出盖板上开设的孔洞;盖板上设置与筒体连接的定位总成
。
7.通过采用上述技术方案,将星型结构进行优化,在法兰内壁安装米字撑,筒体内下部安装配备加劲条的顶隔板,筒体用侧板
、
通长腹板和中间腹板围起来,并用加强筋板加强,对筒体进行组装定位,降低了托架的制造难度
。
8.优选的,筒体由各分段卷圆成型后拼接而成
。
9.通过采用上述技术方案,筒体分段制造,将一个大的筒体分成若干小部分进行制造,每个小部分的制造可以同时进行,提高生产效率
。
10.优选的,筒体侧壁开设人孔
。
11.通过采用上述技术方案,通过侧壁的人孔进行检修,确保设备正常运行;
优选的,侧板上通过三角筋板安装外侧劲板
。
12.通过采用上述技术方案,外侧劲板和四周侧板之间用三角筋板连接,增加外侧劲板和四周侧板之间的连接强度,提高结构强度
。
13.优选的,顶隔板中央有一个
l
型的楼梯口
。
14.通过采用上述技术方案,在
l
型的楼梯口上设置钢制楼梯,方便人员上下检修
。
15.优选的,底板上圆孔外围设置多个洞口
。
16.通过采用上述技术方案,在底板上开设各个洞口,便于给加强筋板定位的同时,减少运输托架的自重,并节省材料,节约制造成本
。
17.田字型海上风电塔筒运输船用托架的施工工艺,包括以下步骤:步骤一
、
零件板分断拼接;步骤二
、
田字型运输托架筒体合拢件组装;筒体合拢件组装采用反造法制作;
①
、
装配定位焊法兰;法兰板下料时厚度增加焊后机加工余量,法兰圆环板采用分断对接,拼接成型后整体机加工,法兰内壁焊接米字撑;
②
、
装配定位焊筒体;筒体采取分段卷圆,各分段卷圆成型后拼接而成;各分段筒体分别吊装定位在法兰板上,采用工装控制其变形;筒体的人孔在放样下料切割时喷粉划线,卷圆成型后再进行人孔的开设;筒体与法兰之间的角接焊缝要求为局部熔透
pp
,采用双面坡口焊接形式;
③
、
装配定位顶隔板;顶隔板和加劲条首先合拢成小件,顶隔板与加劲条之间角接焊缝要求采用双面角焊缝焊接形式;然后分块组装定位顶隔板合拢件,先焊接顶隔板与筒体壁板之间的平面位置角焊缝,反面仰角位置的角焊缝和顶隔板分断对接焊缝待筒体翻身后焊接;
④
、
装配定位焊翻身支撑;定位安装筒体翻身的米字撑,控制筒体翻身变形,其米字撑在翻身后整体组装前拆除;步骤三
、
田字型运输托架a分块组装焊接;
①
、a
分块组装胎架设置;
②
、
底板和中间腹板组装定位;底板和中间腹板组装吊装至胎架上后采用临时工装措施加以定位焊接,两侧底板和中间腹板之间的角接焊缝要求采用双面角焊缝焊接形式;
③
、
底封板组装定位;底封板和加劲条首先合拢成小件,底封板与其加劲条之间采用双面角焊缝焊接;然后吊装底封板合拢件定位焊接,底封板合拢件周围与底板之间的角接焊缝要求为局部熔透
pp
,采用单面坡口焊接形式;
④
、
筒体合拢件组装定位;依次吊装定位筒体合拢件组装焊接,筒体合拢件与底板之间的角接焊缝要求为局部熔透
pp
,采用双面坡口焊接形式;
⑤
、
筒体的加强筋板组装定位;依次吊装加强筋板组装焊接,加强筋板与底板及盖板之间的角接焊缝要求采用双面角焊缝要求;定位总成对应的加强筋板与底板及盖板之间的角接焊缝要求为局部熔透
pp
,采用双面坡口焊接形式;加强筋板与筒体
、
中间腹板
、
周围侧板之间的角接焊缝要求为局部熔透
pp
,采用双面坡口焊接形式,无法双面焊时采用单面坡口焊接形式;
⑥
、
侧板组装定位;两侧两块通长腹板之间的接长的侧板均需先接长后组装定位
焊接;底板和侧板之间的角接焊缝要求采用双面角焊缝焊接形式;侧板与盖板以及自身组合之间的角接焊缝要求均为局部熔透
pp
,采用单面坡口焊接形式;
⑦
、
盖板组装定位;依次吊装盖板装配定位,盖板与侧板及筒体之间的角接焊缝为局部熔透
pp
,采用单面坡口焊接形式,反面采用角焊缝加强;盖板分块吊装定位,定位校验合格后焊接其分断拼接位置对接缝,对接焊缝采用垫板焊对接形式;
⑧
、
外侧劲板和三角筋板组装定位;外侧劲板和三角筋板与构架之间的角接焊缝为局部熔透
pp
,采用双面角焊缝焊接形式;
⑨
、
定位总成组装;定位总成合拢件与构架之间焊缝要求采用双面角焊缝形式;
⑩
、b
分块组装参照a分块的组装步骤,a和b两个分块组装检验完成后分块运输至发运港,通过焊接的形式固定在海上重型运输船的甲板上合并对接成田字型海上风电塔筒运输船用托架整体发运
。
18.通过采用上述技术方案,田字型海上风电塔筒运输船用托架的施工工艺,通过对筒体装配定位的顶隔板和米字撑,筒体合拢件通过加强筋板定位在中间腹板
、
侧板
、
通长腹板围起来的空间中,在侧板上焊接外侧劲板,外侧劲板用三角筋板定位加固,然后盖上盖板,最后焊接定位总成,对该圆盘式结构节点进行了优化设计,降低了该托架的焊接制造难度,为后续大型船用海绑件
、
圆形回转件制作提供工艺支持
。
19.本发明相对于现有技术,具有以下有益效果:
1.
本发明将星型结构进行优化,在筒体内下部安装配备加劲条的顶隔板,筒体用侧板
、
通长腹板和中间腹板围起来,并用加强筋板加强,对筒体进行组装定位,降低了托架的制造难度
。
20.2.
本发明外侧劲板和四周侧板之间用三角筋板连接,增加外侧劲板和四周侧板之间的连接强度,提高结构强度
。
21.3.
本发明田字型海上风电塔筒运输船用托架的施工工艺,通过对筒体装配定位的顶隔板和米字撑,筒体合拢件通过加强筋板定位在中间腹板
、
侧板
、
通长腹板围起来的空间中,在侧板上焊接外侧劲板,外侧劲板用三角筋板定位加固,然后盖上盖板,最后焊接定位总成,对该圆盘式结构节点进行了优化设计,降低了托架的焊接制造难度,很好的控制了焊接过程中的结构变形,焊接精度高,为后续大型船用海绑件
、
圆形回转件制作提供工艺支持
。
附图说明
22.图1为本发明托架分块示意图
。
23.图2为本发明盖板分断图
。
24.图3为本发明底板分断图
。
25.图4为本发明通长腹板分断图
。
26.图5为本发明筒体展开分断图
。
27.图6为本发明筒体合拢件组装第1步示意图
。
28.图7为本发明筒体合拢件组装第3步示意图
。
29.图8为本发明筒体合拢件组装第4步示意图
。
30.图9为本发明筒体合拢件组装第5步示意图
。
31.图
10
为本发明筒体焊接示意图
。
32.图
11
为本发明田字型运输托架a分块组装焊接第1步示意图
。
33.图
12
为本发明田字型运输托架a分块组装焊接第2步示意图
。
34.图
13
为本发明田字型运输托架a分块组装焊接第4步示意图
。
35.图
14
为本发明田字型运输托架a分块组装焊接第5步示意图
。
36.图
15
为本发明田字型运输托架a分块组装焊接第6步示意图
。
37.图
16
为本发明田字型运输托架a分块组装焊接第7步示意图
。
38.图
17
为本发明田字型运输托架a分块组装焊接第8步示意图
。
39.图
18
为本发明田字型运输托架a分块组装焊接第9步示意图
。
40.图中,
1.
星型结构
,2.
筒体
,3.
加强筋板
,4.
法兰
,5.
米字撑
,6.
顶隔板
,7.
加劲条
,8. 底封板
,9.
底板
,10.
侧板
,11. 中间腹板
,12.
盖板
,13.
孔洞
,14.
外侧劲板
,15.
定位总成
,16.
筒体合拢件
,17. 通长腹板
, 18.
三角筋板
,19.
楼梯口
,20.
洞口
,21.
人孔
,22.
分块位置线,
23.
胎架,
24.
支墩
。
实施方式
41.田字型海上风电塔筒运输船用托架,包括四个相接的星型结构1,每个星型结构1由中心的筒体2和加强筋板3组装而成
。
42.筒体2设置在法兰4的法兰板上,筒体2内下部设置顶隔板6,顶隔板6上设有加劲条7,增加顶隔板的强度,形成筒体合拢件
16。
法兰4内壁用米字撑5支撑,此米字撑5待整体组装后拆除
。
43.筒体合拢件
16
通过底封板8设置在底板9上
。
法兰4位于底面
。
底板9的横向边上设置通长腹板
17
,底板9的纵向边上设置中间腹板
11
,底板9的两侧边上设置侧板
10。
筒体2外壁周向设置加强筋板
3。
侧板
10、
通长腹板
17
和中间腹板
11
均与加强筋板3连接
。
侧板
10、
通长腹板
17
上盖设盖板
12
,筒体2穿出盖板
12
上开设的孔洞
13
;侧板
10
外侧设置外侧劲板
14。
四块安装有筒体2的底板9相接形成星型结构
1。
盖板
12
上设置与筒体2连接的定位总成
15。
本技术将星型结构1进行优化,在筒体2内下部安装配备加劲条7的顶隔板6,筒体2用侧板
10、
通长腹板
17
和中间腹板
11
围起来,并用加强筋板3加强,对筒体2进行组装定位,降低了托架的制造难度
。
44.筒体2由各分段卷圆成型后拼接而成
。
筒体2分段制造,将一个大的筒体2分成若干小部分进行制造,每个小部分的制造可以同时进行,提高生产效率
。
45.筒体2侧壁开设人孔
21。
通过侧壁的人孔
21
进行检修,确保设备正常运行
。
46.侧板
10
上通过三角筋板
18
安装外侧劲板
14。
外侧劲板
14
和四周侧板
10
之间用三角筋板
18
连接,增加外侧劲板
14
和四周侧板
10
之间的连接强度,提高结构强度
。
47.顶隔板6中央有一个
l
型的楼梯口
19。
在
l
型的楼梯口
19
上设置钢制楼梯,方便人员上下检修
。
48.底板9上圆孔外围设置多个异形的洞口
20。
在底板9上开设各个异形的洞口
20
,便于给加强筋板3定位的同时,减少运输托架的自重,并节省材料,节约制造成本
。
49.如图1所示,田字型海上风电塔筒运输船用托架的施工工艺,将托架拆分成a分块
和b分块后,通过焊接的方式固定在船甲板上合并对接成田字型海上风电塔筒运输船用托架整体
。
田字型海上风电塔筒运输船用托架结构复杂,外形尺寸较大,制作和现场安装要求较高
。
在提高单件精度,确保整体精度的前提下确定“化整为零,精益求精”的指导思想
。
首先沿着田字型海上风电塔筒运输船用托架中间分块位置线
22
分断拆分成a和b两个分块制作发运,单块的最大尺寸长
x
宽
x
高:
27405mmx13850mmx5055mm,
单净重约
280t。
其次超宽超长的零件板进行工厂分断,然后拼接接长接宽,将每块板的成形做到图纸尺寸要求,并在钢胎架上进行测量检验其平整度
。
因其结构复杂,外形尺寸较大,所以零件板采用预处理钢板下料切割
。
50.a
分块组装
,
包括以下步骤:步骤一
、
如图
2-5
所示,零件板分断拼接
. 超宽超长零件板(底板
9、
盖板
12、
通长腹板
17、
底封板
8、
顶隔板
6、
筒体2)放样时均需断料,零件板拼接时考虑组装情况分部吊装分段对接
。
盖板
12
对接焊吊装定位后焊接
。
51.步骤二
、
田字型运输托架筒体合拢件
16
组装;筒体合拢件
16
组装采用反造法制作;第1步:如图6所示,在稳定牢固平整的平台板上设置6个支墩
24
(高度
600~800mm
),其平面度控制
1mm。
52.第2步:装配定位焊法兰
4。
法兰板下料时厚度增加
10mm
焊后机加工余量,法兰圆环板采用分断对接,拼接成型后整体机加工,法兰4定位采用米字撑5定位焊控制其变形
。
53.第3步:如图7所示,装配定位焊筒体
2。
筒体2采取分段卷圆,各分段卷圆成型后拼接而成
。
各分段筒体2分别吊装定位在法兰板上,采用工装控制其变形
。
筒体2的人孔
21
在放样下料切割时喷粉划线,卷圆成型后再进行人孔
21
的开设
。
筒体2与法兰4之间的角接焊缝要求为局部熔透(
pp
),采用双面坡口焊接形式
。
54.第4步:如图8所示,装配定位顶隔板
6。
顶隔板6和加劲条7首先合拢成小件,顶隔板6与加劲条7之间角接焊缝要求采用双面角焊缝焊接形式
。
然后分块组装定位顶隔板合拢件,先焊接顶隔板6与筒体2壁板之间的平面位置角焊缝,反面仰角位置的角焊缝和顶隔板6分断对接焊缝待筒体2翻身后焊接
。
55.第5步:如图9所示,装配定位焊翻身支撑
。
定位安装筒体2翻身的米字撑5,控制筒体2翻身变形,其米字撑5在翻身后整体组装前拆除
。
56.如图
10
所示,筒体2与法兰4的焊接
。
筒体2组装定位检验合格后先焊接筒体2与法兰4的角接焊缝,由四名焊工(
a、b、c、d
)同时按照下图所示先焊接筒体外侧第一层打底焊缝,后焊接筒体2内侧第一层打底焊缝,然后每层焊缝先外后内交错焊接
。
焊接电流严格按照
wps
进行焊接,焊接时控制层间温度不大于
250℃
,超过层间温度时,待冷却后再焊接
。
焊接过程中监测法兰4平面度的变化情况,焊缝每焊接3层时,需要检查一次
。
57.步骤三
、
田字型运输托架a分块组装焊接;第1步,如图
11
所示,a分块组装胎架设置
。
胎架的具体定位尺寸需根据运输专用平板车尺寸设置,图示为主体胎架
23
位置,其余零件需要设置部分辅助胎架,组装胎架设置需稳定高强
。
胎架
23
总体水平度要求控制公差
±
1mm
,其中间三个胎架支腿在构件发运时拆除,方便平板车托运
。
58.第2步,如图
12
所示,底板9和中间腹板
11
组装定位
。
底板9和中间腹板
11
组装吊装至胎架上后采用临时工装措施加以定位焊接,两侧底板9和中间腹板
11
之间的角接焊缝要
求采用双面角焊缝焊接形式
。
59.第3步,底封板8组装定位
。
底封板8和加劲条7首先合拢成小件,底封板8与其加劲条7之间采用双面角焊缝焊接
。
然后吊装底封板合拢件定位焊接,底封板合拢件周围与底板9之间的角接焊缝要求为局部熔透(
pp
),采用单面坡口焊接形式
。
60.第4步,如图
13
所示,筒体合拢件
16
组装定位
。
依次吊装定位筒体合拢件(
16
)组装焊接,筒体合拢件
16
与底板9之间的角接焊缝要求为局部熔透(
pp
),采用双面坡口焊接形式
。
筒体合拢件与底板9的焊接顺序参照筒体2与法兰4的焊接顺序
。
61.第5步,如图
14
所示,筒体2的加强筋板3组装定位
。
依次吊装加强筋板3组装焊接,筒体2外侧的加强筋板3与底板9及盖板
12
之间的角接焊缝要求采用双面角焊缝要求
。
定位总成
15
对应的加强筋板3与底板9及盖板
12
之间的角接焊缝要求为局部熔透(
pp
),采用双面坡口焊接形式
。
通过筒体2外壁一圈的加强筋板3加强风电塔筒运输定位
。
62.加强筋板3与筒体
2、
中间腹板
11、
周围侧板
10
之间的角接焊缝要求为局部熔透(
pp
),采用双面坡口焊接形式,无法双面焊时可采用单面坡口焊接形式
。
63.第6步,如图
15
所示,侧板
10
组装定位
。
两侧通长腹板
17
和通长腹板
17
之间的厚薄板接长的侧板
10
均需先对接接长后组装定位焊接
。
底板9和侧板
10
之间的角接焊缝要求采用双面角焊缝焊接形式
。
64.侧板
10
与盖板
12
以及自身组合之间的角接焊缝要求均为局部熔透(
pp
),采用单面坡口焊接形式
。
65.第7步,如图
16
所示,盖板
12
组装定位
。
依次吊装盖板
12
装配定位,盖板
12
与侧板
10
及筒体2之间的角接焊缝为局部熔透(
pp
),采用单面坡口焊接形式,反面采用角焊缝加强
。
盖板
12
分块吊装定位,定位校验合格后焊接其分断拼接位置对接缝,对接焊缝采用垫板焊对接形式
。
66.第8步,如图
17
所示,外侧劲板
14
和三角筋板
18
组装定位
。
外侧劲板
14
和三角筋板
18
与构架之间的角接焊缝为局部熔透(
pp
),采用双面角焊缝焊接形式
。
67.第9步,如图
18
所示,定位总成
15
组装
。
定位总成
15
预先小合拢,定位总成
15
自身组合之间的焊缝要求采用双面角焊缝焊接形式,定位总成合拢件与构架之间焊缝要求采用双面角焊缝形式
。
68.第
10
步,b分块组装参照a分块的组装步骤,a和b两个分块组装检验完成后分块运输至发运港,通过焊接的形式固定在
sw7
海上重型运输船的甲板上合并对接成田字型海上风电塔筒运输船用托架整体发运
。
69.本技术田字型海上风电塔筒运输船用托架的施工工艺,通过对筒体2装配定位的顶隔板6和米字撑5,筒体合拢件
16
通过加强筋板3定位在中间腹板
11、
侧板
10
和通长腹板
17
围起来的空间中,在侧板
10
上焊接外侧劲板
14
,外侧劲板
14
用三角筋板
18
定位加固,然后盖上盖板
12
,最后焊接定位总成
15
,对该圆盘式结构节点进行了优化设计,降低了托架的焊接制造难度,很好的控制了焊接过程中的结构变形,焊接精度高,为后续大型船用海绑件
、
圆形回转件制作提供工艺支持
。
70.该托架用于运输变径型海上风电塔筒,运输托架以焊接形式安装在海上重型运输船的甲板上整体发运,辅助完成海上风电设施安装的工作
。
此船为世界上最大和最具创新性的海上风力发电基础设施安装船,将为全球碳中和和风电发电领域持续贡献力量
。
71.尽管已经示出和描述了本发明的实施例,对于本领域的普通技术人员而言,可以理解在不脱离本发明的原理和精神的情况下可以对这些实施例进行多种变化
、
修改
、
替换和变型,本发明的范围由所附权利要求及其等同物限定
。